Rechampir brushes – the paintbrush for all those difficult to reach areas Some background information……
How are paint rollers made?
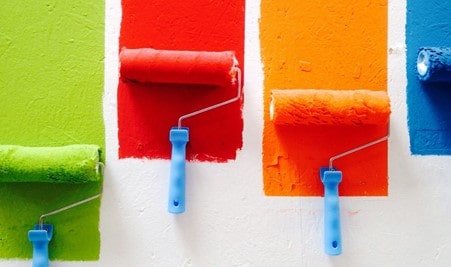
If you’ve ever wondered ” How are paint rollers made?” you’ve come to the right place. Read on to find out more about how paint rollers are made today.
Thermofusion is a method used to fix the roller fabric to its plastic inner core.
In the past rollers were traditionally made by using an adhesive spread over the surface of the inner tube, that then had the roller fabric wound on to it. This process was used for many years but came with some drawbacks, namely if the adhesive failed then the fabric would come away from the inner core. Adhesives are also affected by solvents, which caused issues when the roller was used in more industrial coatings.
Thermofusion is now mostly used in the production of rollers, there are two main types of process.
The original thermo process was to use a naked gas flame to melt the surface of the plastic tube the fabric would then be wound on to the molten surface. Once cooled the tube and fabric became one piece. This overcame the problems of poor adhesion and also allowed the roller to be used in stronger solvents.
The second and more recent improvement to the thermofusion process is not to use a naked flame to melt the tube surface. This part of the process is now done in a sealed unit where the same material as the plastic tube is melted under control. The molten plastic is then applied on to the inner tube surface and the fabric is wound directly on to it. The end result is exactly the same with the inner tube and fabric becoming one piece. The major benefits of this process are that there is no dangerous naked flame, there are no noxious fumes and because the molten material is at a controlled temperature there is a greatly reduced chance of the inner core distorting, meaning better fit for the roller refills to the frame.